ばねは用途や環境によって形、材料、大きさが違います。材料の形状は大きく分けて線材と板材があり、また成形方法は材料を熱して加工する熱間成形と常温で加工する冷間成形があります。冷間成形は熱間成形に対する呼称で冷やして加工するものではありません。
ここでは圧縮コイルばね冷間成形の製造工程に沿ってばねの知識をご案内します。
※一般的な工程で製品により工程の増減、順序は変わります。
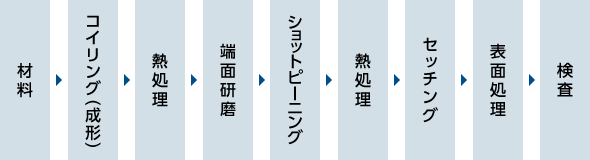
材料
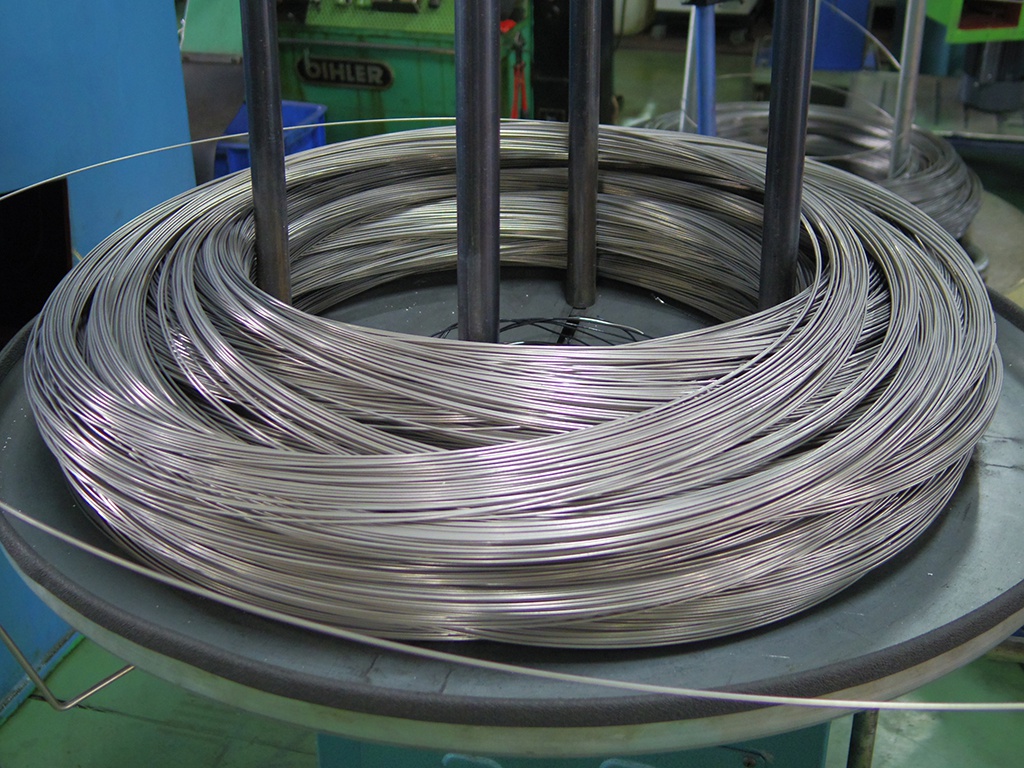
ピアノ線、硬鋼線、ステンレス線、オイルテンパー線、りん青銅などがばね材として一般的に使用されています。
ばね設計の際、要求品質を満足し、かつコストをおさえるという点において材料選びは重要です。
各材料には耐疲労性、耐食性、非磁性などそれぞれに特徴があり、また同時に価格の幅が大きくあります。
そのままでは要求品質を満たさない材料でもショットピーニングによる耐疲労性の向上、メッキ処理による耐食性向上など後の工程において補うことができます。
一般的な材料とは別に各線材メーカーが開発したより高強度なもの、真直処理されたものなどもあります。
材料選びには知識と経験が必要です。ご相談ください。
コイリング
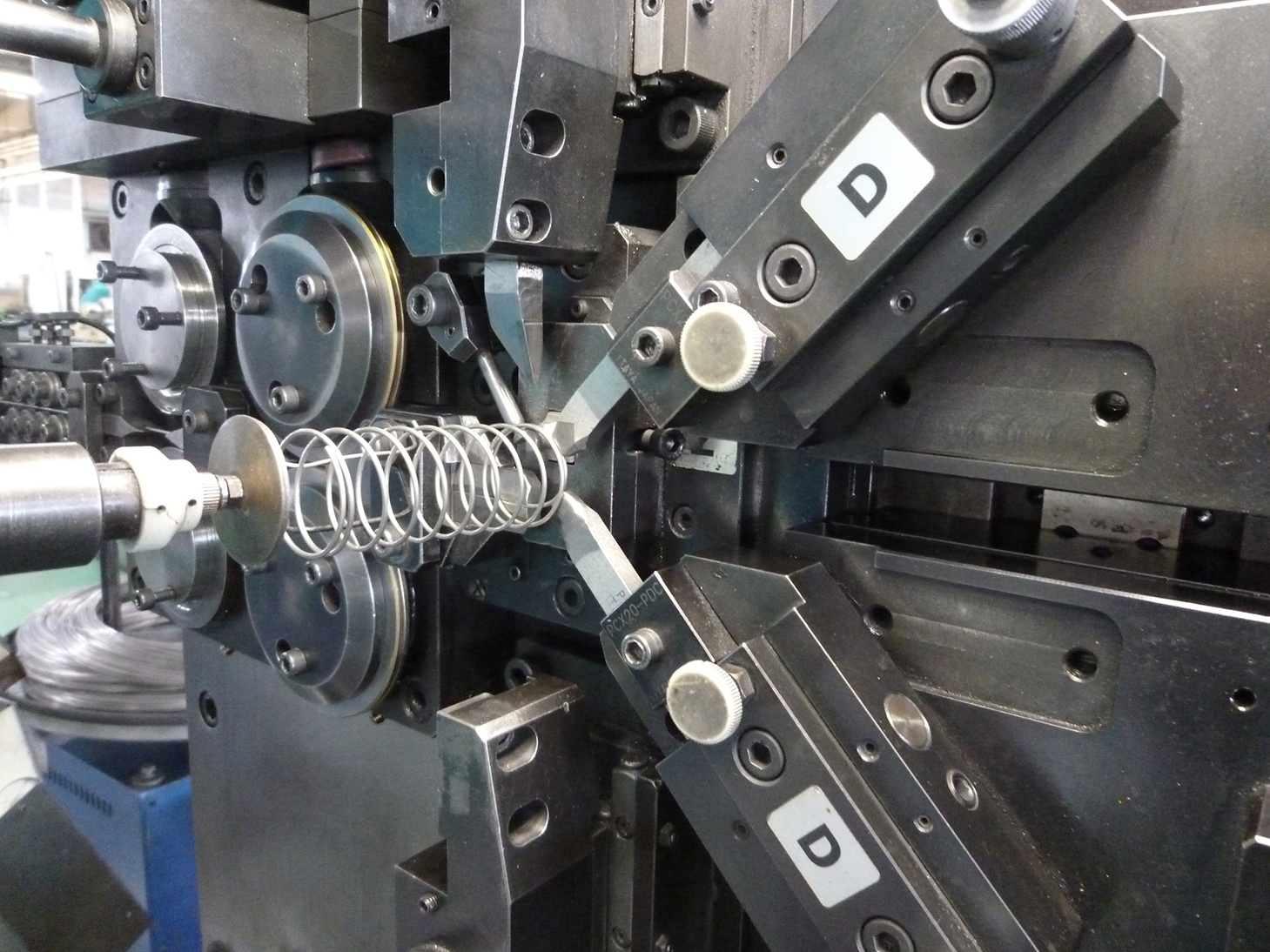
コイリングマシンを使用して材料をコイル状(らせん状)に成形します。
当社では随時最新設備を導入し高精度ばねを生産しています。
熱処理(低温焼きなまし)
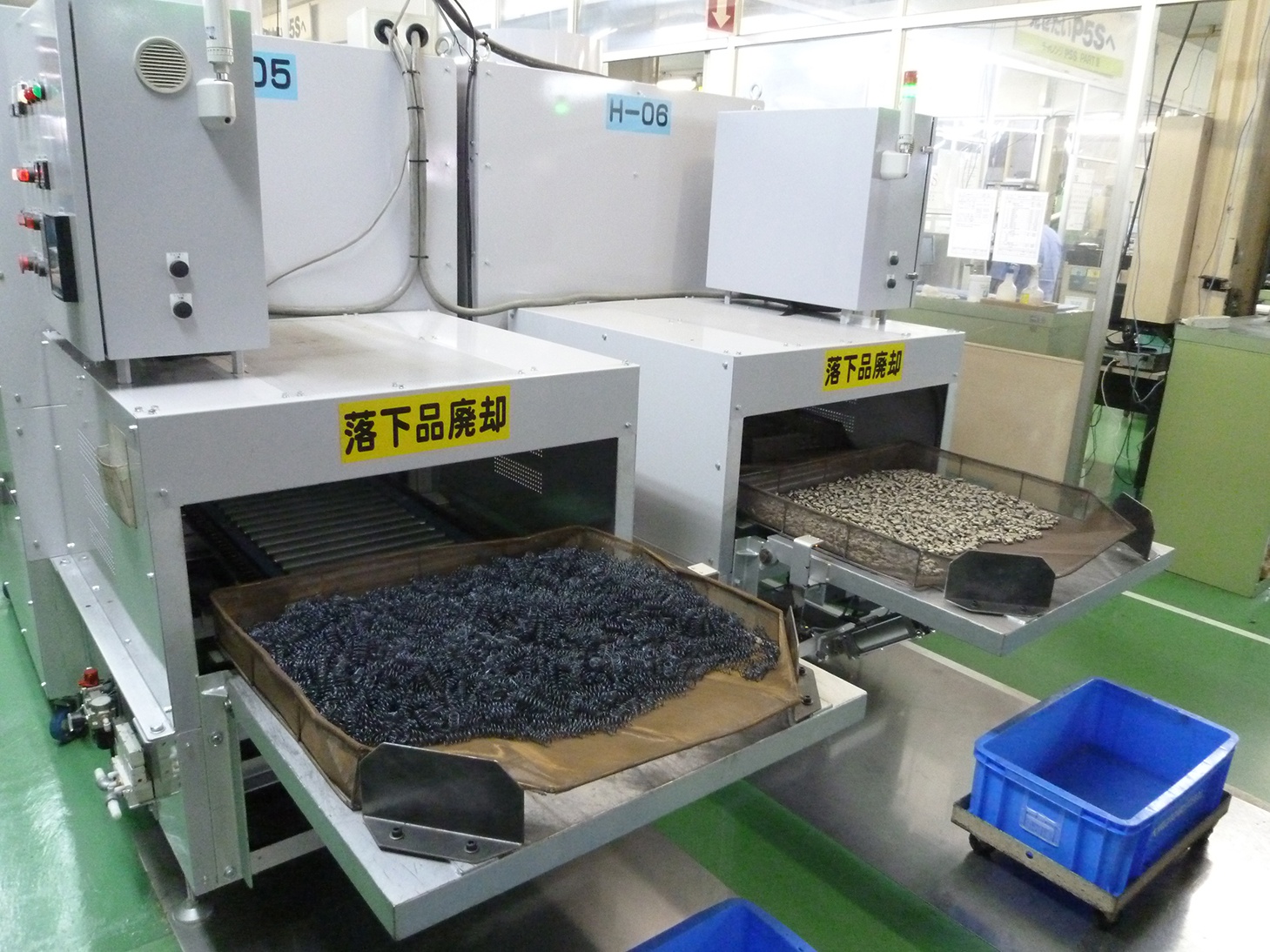
熱処理の目的は冷間成形加工に伴う有害な残留応力(元の形に戻そうとする力)を取り除き形状を安定させることです。
また、残留応力が残っているとへたりや折損がおこりやすくなります。
材料によって温度条件など熱処理方法を変えます。熱処理によってばねの寸方は変化しますが材料の種類によって寸法変化は違い一定ではありません。
ショットピーニング後の熱処理は弾性の回復(疲労強度向上)を目的として行います。
端面研削
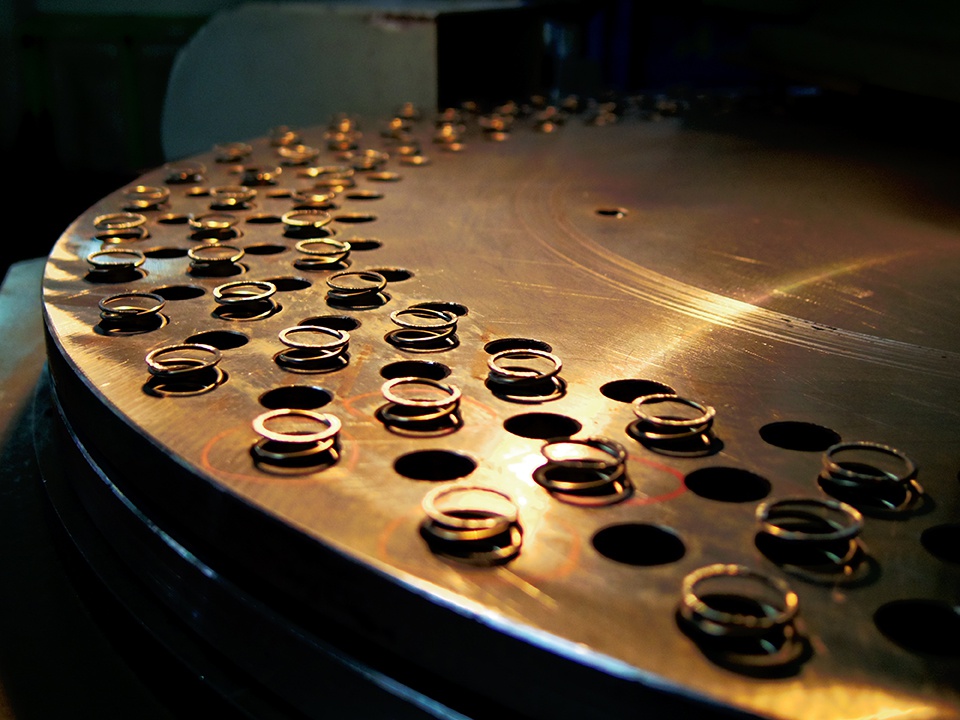
一般的には荷重の偏りや相手部品の損傷を防ぐなどの目的で端面を研削処理して平坦にします。
線径の小さいもの(細い線材)は荷重の偏りや相手物への影響が少ないので研削を省略する場合もあります。
ショットピーニング
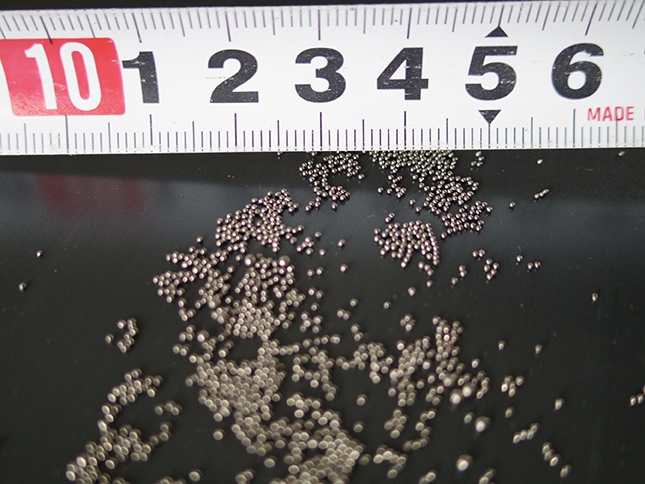
ショット金属球
ショットピーニングの目的は耐疲労性の向上です。
小さな金属球を高速度かつ連続的に打ち付けることにより表面層を加工硬化させる表面加工です。
これにより表面層には圧縮残留応力が残り、繰返し荷重に対して圧縮残留応力が相殺する形で作用し疲れ強さが増加します。加工硬化している部分は表面層だけで、材料自体の引張り強さなどには大きな影響は与えません。
セッチング
セッチングの目的は使用時のへたりを極力少なくすることです。
成形・熱処理後の最終工程近くでばね使用方向に最大使用応力以上の荷重を与え塑性変形を行わせる処理です。
使用状況などに応じて加熱した状態でセッチングをしたり、荷重をかけた状態で熱処理をする方法もあります。これをヒートセッチングと言います。
表面処理
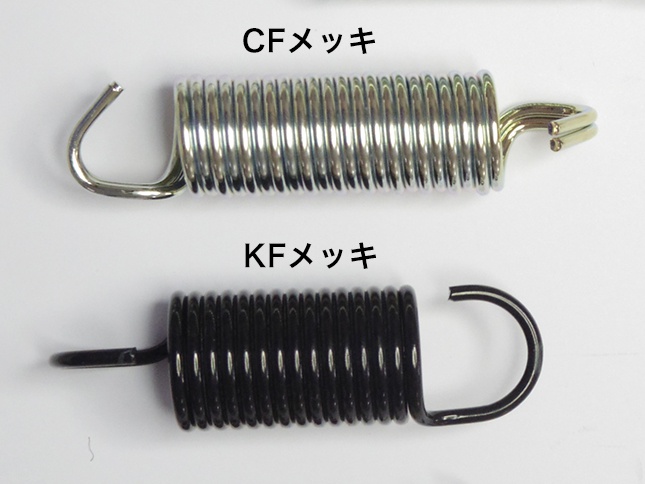
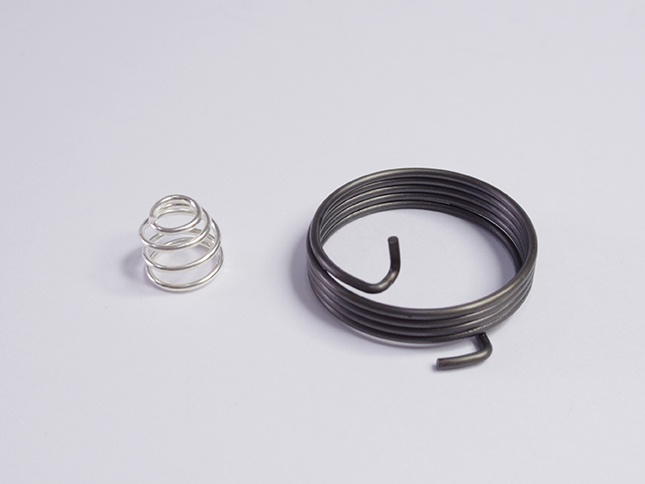
銀メッキ、パーカ加工
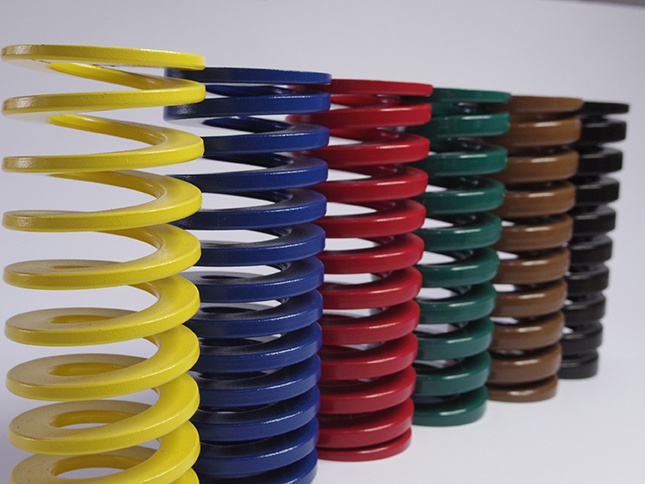
塗装
表面処理の目的は主に鉄鋼素材のばねの腐食を防ぐことです。
他の目的としては外観を良くするためや識別のために表面処理をすることがあります。
腐食防止には単純に防錆油をかける方法の他、塗装、メッキ処理、黒染め、パーカ加工などいろいろな方法があります。目的とコストに応じてご提案いたします。
検査
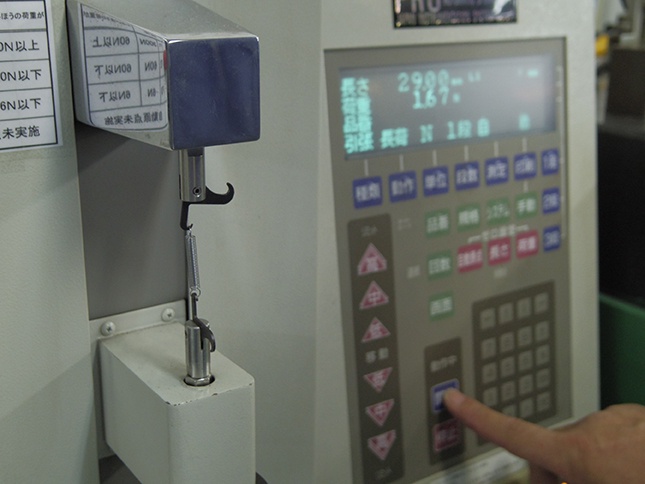
荷重試験機
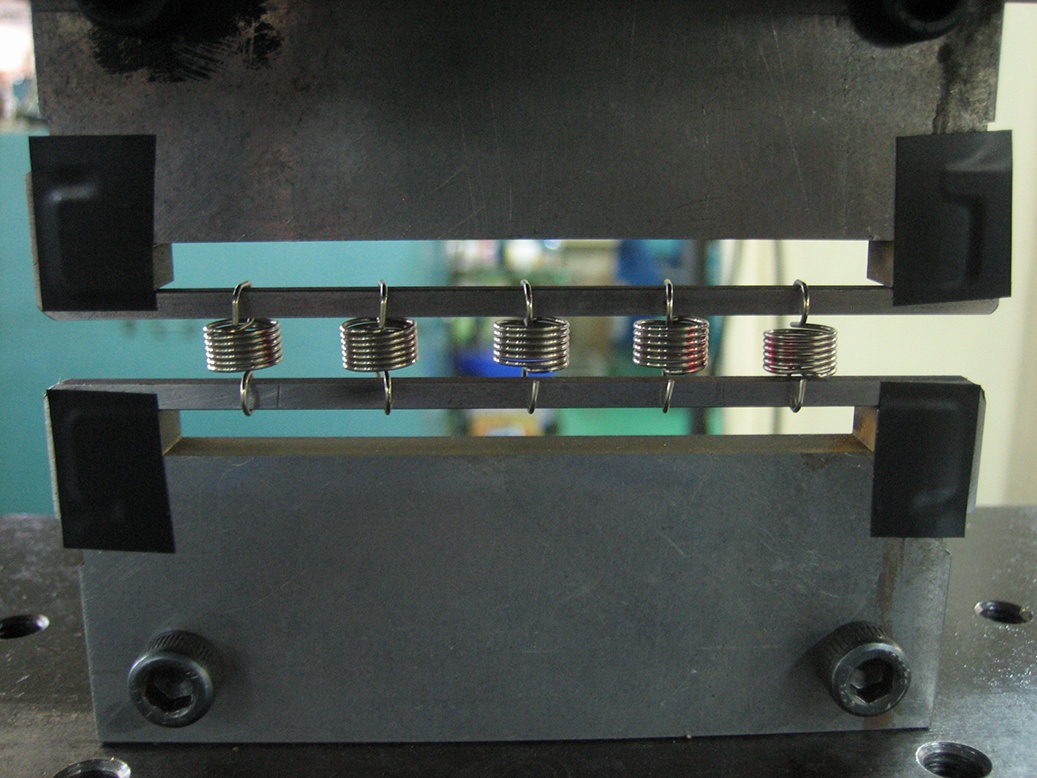
耐久試験機
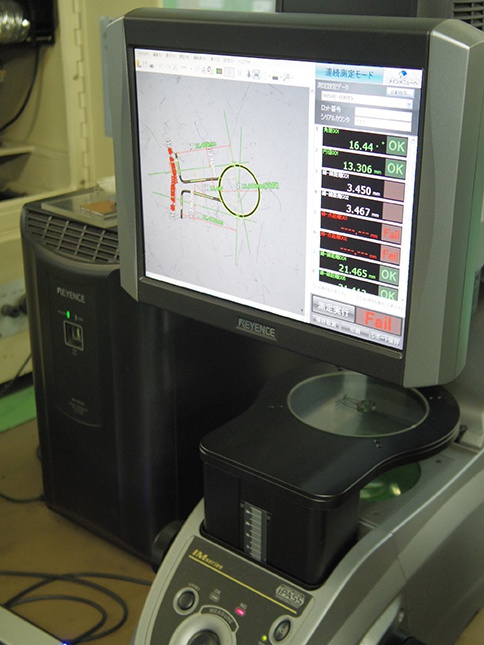
画像寸法測定器
検査項目は線径・内径・外径・自由長・ピッチなどの寸法のほか巻数・ばね定数・荷重や外観、耐久試験があります。また、圧縮ばねは側面に対する端部との直角度、ねじりばねは巻き角度などがあります。
要求品質に応じて検査項目を決定し、その必要精度に応じて検査機器も変わります。
また、重要部品については全点検査を行うこともありますが当然コストはあがります。
ばねの不具合について(折損、へたり、変形など)
ばねの不具合は経年劣化によっておこるものと、何らかの原因があって早期におこるものがあります。
早期におきる不具合は製造メーカーに原因があると思われがちですが不具合が生じる原因はいろいろあります。原因の主なものとして傷、使用環境、設計ミスがあり、また複数の原因が重なっておきる場合もあります。もちろん材料自体に問題があったり、製造工程において発生することもありますが、出荷後の原因を例にあげると、組み付け時に無理があり相手部品と接触して起こる傷、絡んだばねを力任せにほどいたことによる変形、温度・湿度・振動などの使用環境にあっていない材料選びや表面処理などです。
ばねを持つと、つい押したり曲げたりしたくなりますが、それにより変形したり荷重が変化したりします。線径などにもよりますがばねはデリケートな部品です。取り扱いには注意が必要です。
このようなことから不具合の原因追求や、設計の際には相手部品、取扱い方などの組立て時の状況、使用環境を十分に考慮しなければなりません。